- hr@laranaworld.com
- Open Hours: Mon - Fri 8.00 am - 6.00 pm
Warehousing
- Home
- Warehousing
Warehousing
Warehouse organization can often feel like an ongoing struggle. But tidy and well-organized warehouses make the entire process of receiving products, storing them, picking and packing items, and then shipping them to customers more efficient.
Unfortunately, organizing your warehouse operations and keeping them that way can be easier said than done. Each decision you make should optimize your existing space, boost productivity, deliver a better customer experience, and align with your business goals. Here are some tips for keeping your warehouse organized that you can implement.
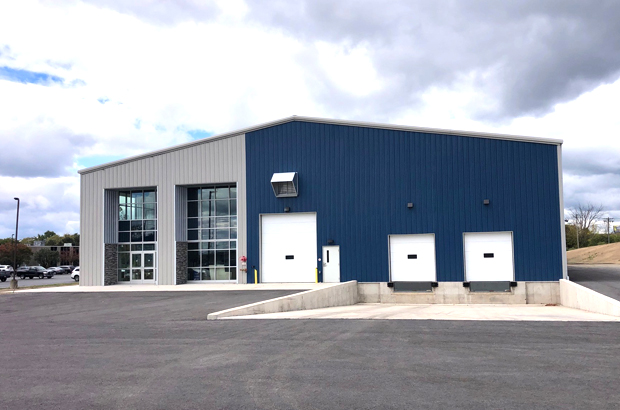
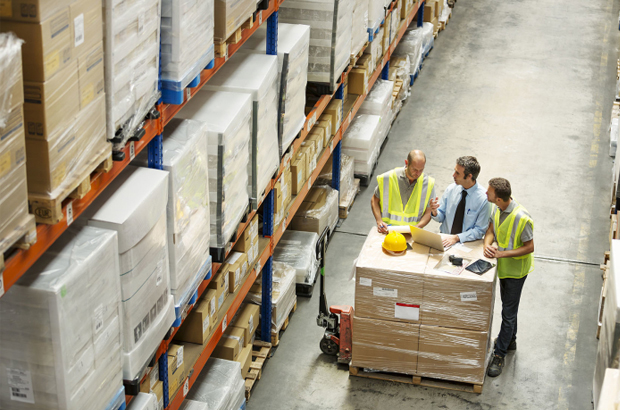
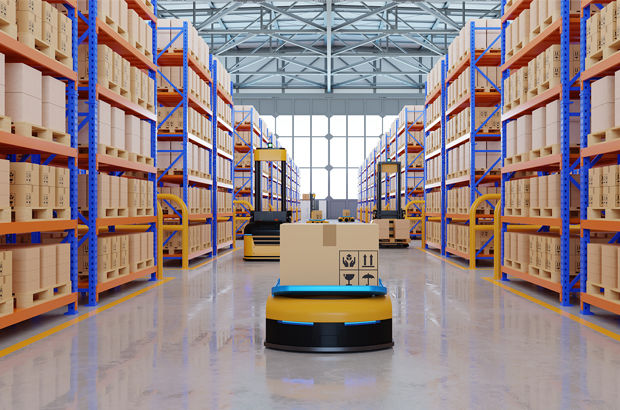


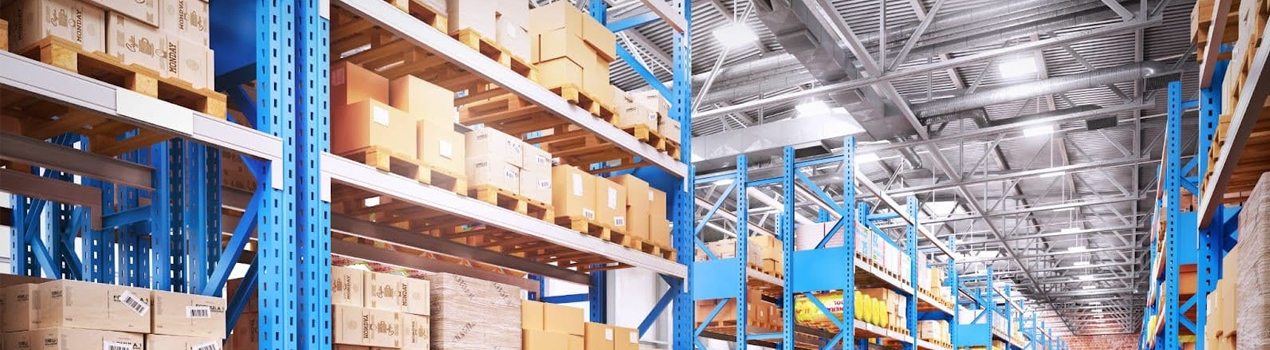
Keep your warehouse clean
Set aside time in every shift to clean work areas. This should be part of every worker’s job description. You should also designate time for organization and deep cleaning activities each week or month.
Consider using lean inventory
When you adopt a lean inventory system, you only have the products you need to fulfill orders on hand. However, make sure you take into consideration any supply chain issues before implementing major changes.
Reduce clutter
No matter what type of inventory system you use, get rid of the clutter in your warehouse. Products and debris in the aisles can be safety hazards, reduce morale, and lead to massive inefficiency.
Assess space and shelf utilization
Understand the ways your warehouse is using its space so that you can make improvements. Specifically, how are containers and shelves being utilized as they relate to the various traffic patterns throughout the building?
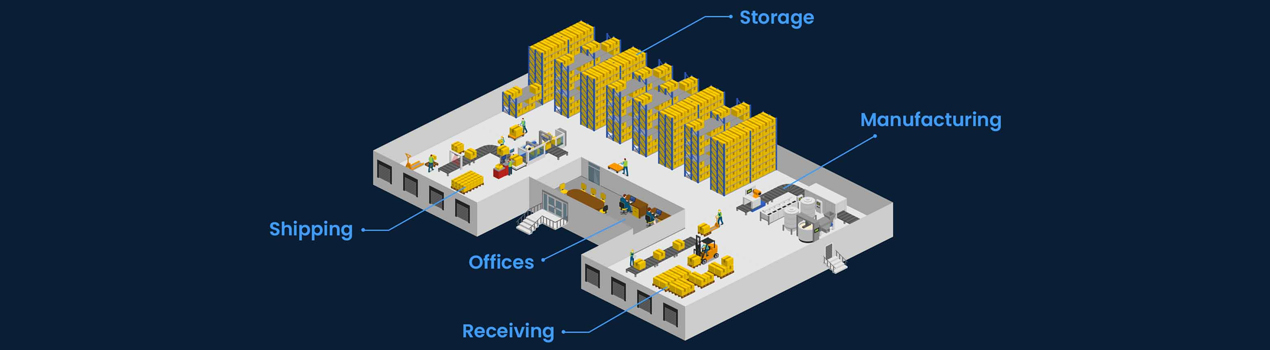
Reevaluate your warehouse design
If your business is growing, as most that handle online sales are, it’s probably a good idea to reevaluate your warehouse design frequently. This is because what worked last year at a certain volume may no longer be efficient. You will need to revise your processes and space requirements as you grow.
Prioritize your SKUs
Your most popular SKUs should be in easy-to-reach physical locations to reduce unnecessary work. Going along with the last recommendation, you’ll want to reassess this often. Popular products can change frequently and shift with the seasons.
Eliminate traffic barriers
Is there anything in your warehouse that is a constant barrier to shipping, receiving, or other activities? Aisles shouldn’t be holding or staging areas or places to leave malfunctioning equipment.
Maximize your available space
Rather than look around for a larger warehouse, explore ways to make better use of the space you already have. Most warehouses fail to properly use their vertical space. Adding a mezzanine or taller storage shelves can significantly add to your available space. You can also use different types of storage units, such as pallet racks and bins.
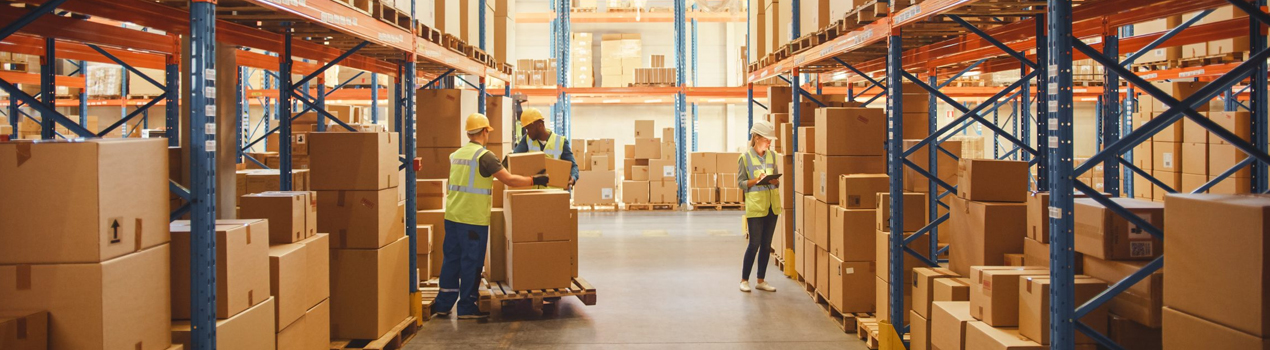
Leverage warehouse technology
Most of today’s warehouses are using technology solutions to gain efficiencies and a competitive edge. These solutions also help keep your warehouse organized. The best place to start is with a warehouse management system (WMS). You can then add other technology such as RFID tags and automation solutions.
Use a smart labeling system
Manually counting inventory or warehouse assets isn’t efficient. And barcode systems have a lot of limitations. If you want to have the simplest and most efficient labeling system possible, consider implementing RFID tags.
Control your inventory
If you can’t control your inventory, your warehouse is going to be a mess. You can accomplish this through a combination of using the right warehouse layout, a WMS, better processes, RFID tags, and some warehouse automation tools.
Invest in warehouse signage
Once you organize your warehouse, make it simple to navigate with clear signage. Mark the aisles, shelving, rows, and various sections of your warehouse. Create a map so that it is easier to place things where they belong.
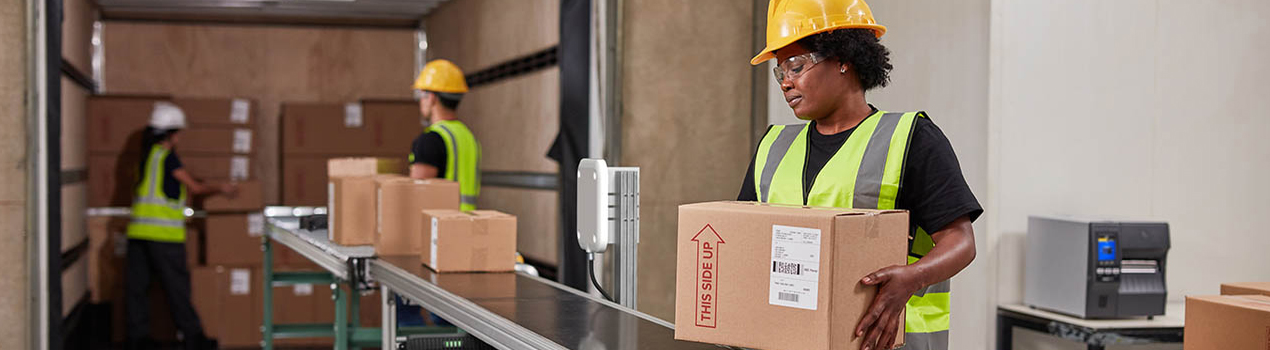
Plan your receiving area
Receiving is a vital part of your warehouse operations. A lot of errors can happen in this part of the business. To avoid problems, plan your physical space wisely. Make sure there is plenty of space to account for all of the truckloads of inventory your warehouse will receive.
Create receiving policies and procedures
Your receiving area is a place where injuries can happen, and people can abscond with products. Create some strict receiving policies and procedures with regards to cleanliness, tidiness, and security. And then train your staff on them.
Set aside a space for reverse logistics
Remember that you will also have a percentage of your sold products come back into the warehouse through returns, recalls, and recycling programs. If you don’t set aside a staging area for reverse logistics, you can create some backlogs and wasted space.
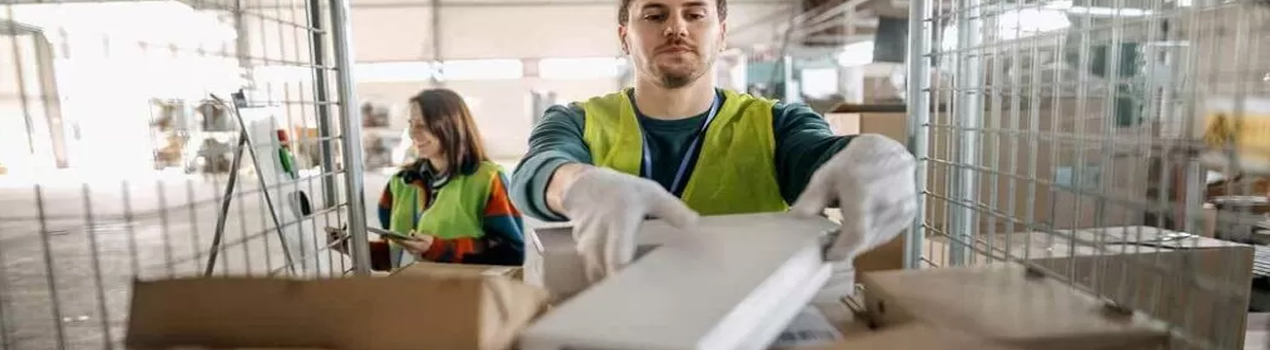
Make bins easier to access
If workers struggle to access storage bins, the picking process will take much longer to complete. In addition, there may also be an increased risk of injury if bins are awkward and hard to reach. Design your bins so that they are simple to see inside.
Reduce travel time
Travel time inside your warehouse can easily account for 50% or more of a worker’s order picking activities. By using cluster and batch order picking strategies, you can reduce some of that walking. When smaller orders are combined, a worker can handle those in a single trip.
Invest in Warehouse Automation
When workers have to travel back and forth to a central location and handle tons of paper, things are likely to get cluttered and possibly confused. Errors will be more common due to employee fatigue, and customer satisfaction will suffer. One solution is to use picking automation solutions, such as wireless headsets and mobile carts. Workers will get order instructions via voice technology, and the system will update in real-time as the products are pulled from shelves.
Warehouses play a vital role in the supply chain. An efficient and lean warehouse will keep your business running more efficiently and provide a better customer experience. With a combination of technology solutions and better processes, your business will realize improved overall results.
General Warehouse Organization
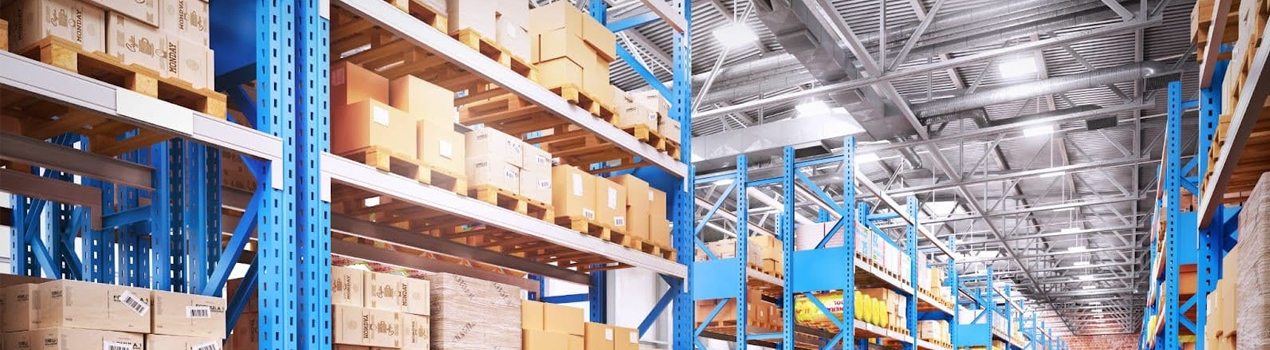
Keep your warehouse clean
Set aside time in every shift to clean work areas. This should be part of every worker’s job description. You should also designate time for organization and deep cleaning activities each week or month.
Consider using lean inventory
When you adopt a lean inventory system, you only have the products you need to fulfill orders on hand. However, make sure you take into consideration any supply chain issues before implementing major changes.
Reduce clutter
No matter what type of inventory system you use, get rid of the clutter in your warehouse. Products and debris in the aisles can be safety hazards, reduce morale, and lead to massive inefficiency.
Assess space and shelf utilization
Understand the ways your warehouse is using its space so that you can make improvements. Specifically, how are containers and shelves being utilized as they relate to the various traffic patterns throughout the building?
Warehouse Layout
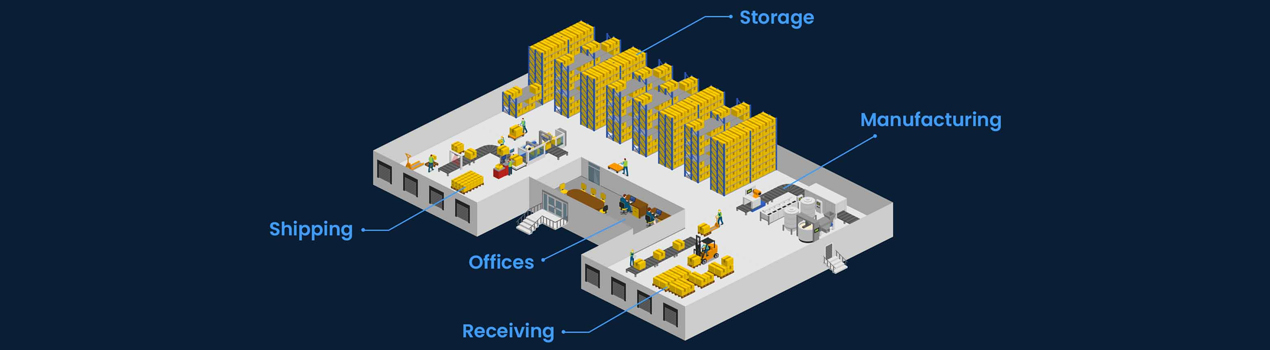
Reevaluate your warehouse design
If your business is growing, as most that handle online sales are, it’s probably a good idea to reevaluate your warehouse design frequently. This is because what worked last year at a certain volume may no longer be efficient. You will need to revise your processes and space requirements as you grow.
Prioritize your SKUs
Your most popular SKUs should be in easy-to-reach physical locations to reduce unnecessary work. Going along with the last recommendation, you’ll want to reassess this often. Popular products can change frequently and shift with the seasons.
Eliminate traffic barriers
Is there anything in your warehouse that is a constant barrier to shipping, receiving, or other activities? Aisles shouldn’t be holding or staging areas or places to leave malfunctioning equipment.
Maximize your available space
Rather than look around for a larger warehouse, explore ways to make better use of the space you already have. Most warehouses fail to properly use their vertical space. Adding a mezzanine or taller storage shelves can significantly add to your available space. You can also use different types of storage units, such as pallet racks and bins.
Warehouse Technology and Labeling
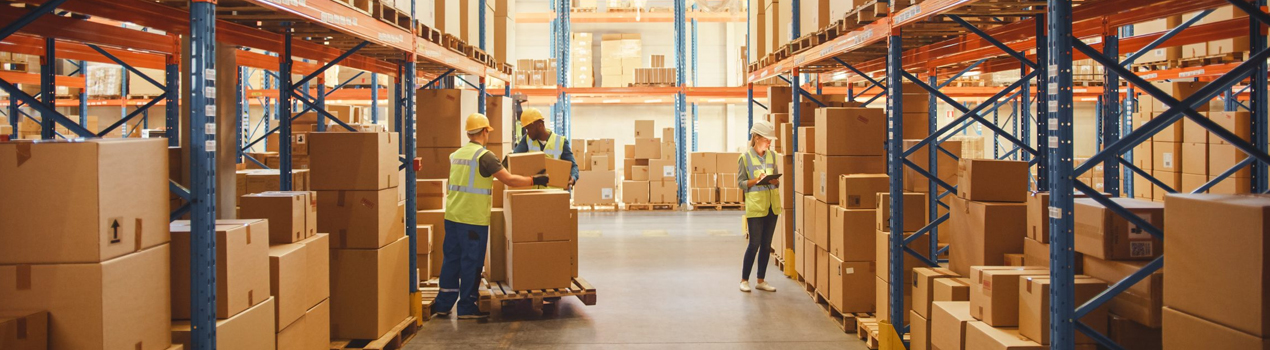
Leverage warehouse technology
Most of today’s warehouses are using technology solutions to gain efficiencies and a competitive edge. These solutions also help keep your warehouse organized. The best place to start is with a warehouse management system (WMS). You can then add other technology such as RFID tags and automation solutions.
Use a smart labeling system
Manually counting inventory or warehouse assets isn’t efficient. And barcode systems have a lot of limitations. If you want to have the simplest and most efficient labeling system possible, consider implementing RFID tags.
Control your inventory
If you can’t control your inventory, your warehouse is going to be a mess. You can accomplish this through a combination of using the right warehouse layout, a WMS, better processes, RFID tags, and some warehouse automation tools.
Invest in warehouse signage
Once you organize your warehouse, make it simple to navigate with clear signage. Mark the aisles, shelving, rows, and various sections of your warehouse. Create a map so that it is easier to place things where they belong.
Warehouse Receiving
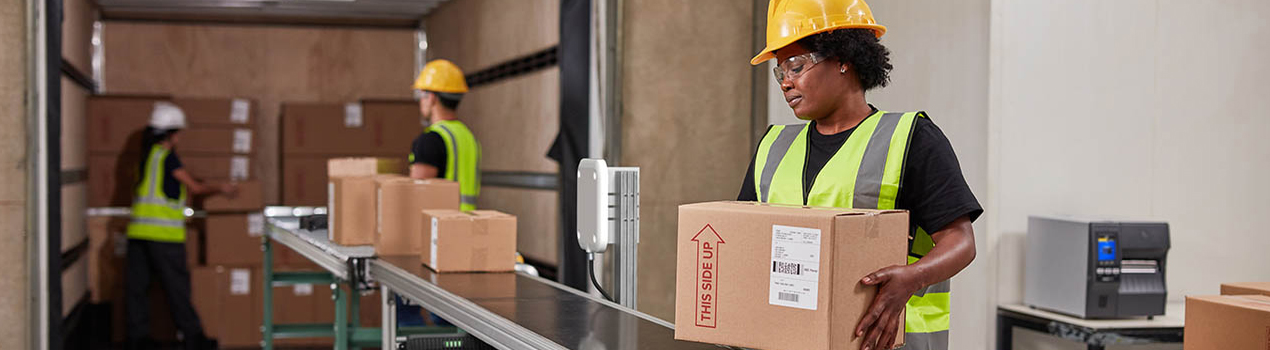
Plan your receiving area
Receiving is a vital part of your warehouse operations. A lot of errors can happen in this part of the business. To avoid problems, plan your physical space wisely. Make sure there is plenty of space to account for all of the truckloads of inventory your warehouse will receive.
Create receiving policies and procedures
Your receiving area is a place where injuries can happen, and people can abscond with products. Create some strict receiving policies and procedures with regards to cleanliness, tidiness, and security. And then train your staff on them.
Set aside a space for reverse logistics
Remember that you will also have a percentage of your sold products come back into the warehouse through returns, recalls, and recycling programs. If you don’t set aside a staging area for reverse logistics, you can create some backlogs and wasted space.
Warehouse Picking
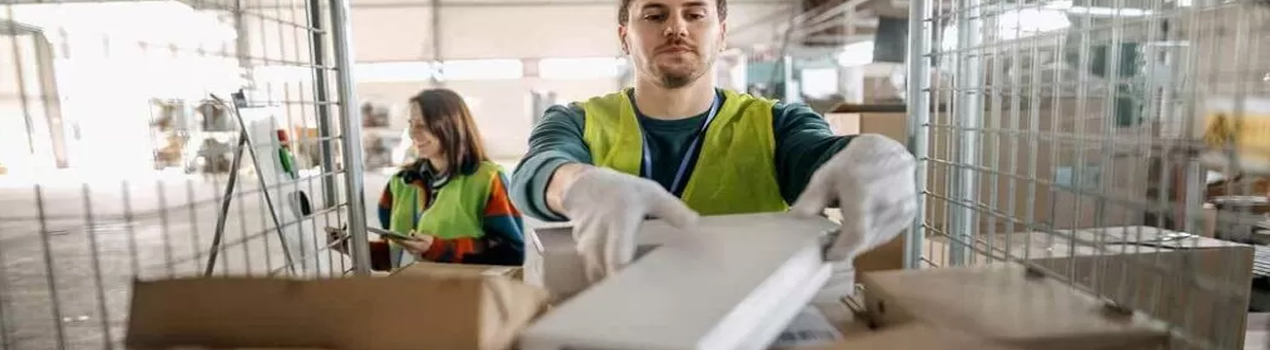
Make bins easier to access
If workers struggle to access storage bins, the picking process will take much longer to complete. In addition, there may also be an increased risk of injury if bins are awkward and hard to reach. Design your bins so that they are simple to see inside.
Reduce travel time
Travel time inside your warehouse can easily account for 50% or more of a worker’s order picking activities. By using cluster and batch order picking strategies, you can reduce some of that walking. When smaller orders are combined, a worker can handle those in a single trip.
Invest in Warehouse Automation
When workers have to travel back and forth to a central location and handle tons of paper, things are likely to get cluttered and possibly confused. Errors will be more common due to employee fatigue, and customer satisfaction will suffer. One solution is to use picking automation solutions, such as wireless headsets and mobile carts. Workers will get order instructions via voice technology, and the system will update in real-time as the products are pulled from shelves.
Warehouses play a vital role in the supply chain. An efficient and lean warehouse will keep your business running more efficiently and provide a better customer experience. With a combination of technology solutions and better processes, your business will realize improved overall results.
Larana Services
- Dubai
- hr@laranaworld.com